Backpack Inspection,Combination of factory self-inspection and 3rd party
The composition and main structure of the introduction
The backpack introduced here refers to the bag used when going out in daily life. Its main function is to solve the problem of consumers’ daily going out or short trip. The product belongs to one kind of bag and is generally made of Oxford cloth, canvas, nylon, leather, etc. In the backpack inspection, understanding the process flow of the product is the core content, so that the inspection can be carried out effectively.At the same time,arrange Factory Audit helps importers to strictly screen products with satisfactory quality.
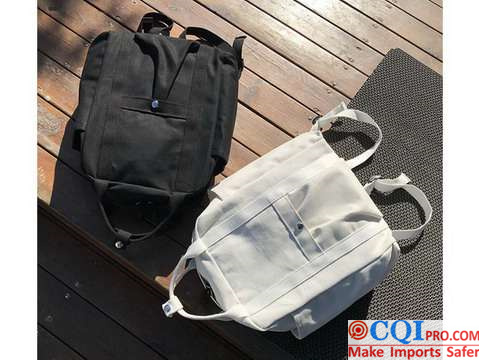
The core manufacturing process
Complete process flow: raw material selection – making sample plate – cutting – table top process – finishing
he important links include:
- Discharging: Discharging is the first working procedure in the production process of bag products. The quality of discharging directly affects the quality of products and the cost of products. The material opening steps are etching, polishing, waxing, punching, molding, punching, cutting, assembling, forming,bending and hot pressing.
- Mesa process: It divides into four categories
1 ) Slice cutting process: the parts and components of the product are cut into certain specifications according to the processing requirements so as to meet the processing requirements of the next working procedure.
2 ) Trimming and inlaying of component edges: It is done on the basis of sheet edges and it is also the basis of stitching. The trimming of the edges usually includes dyed edges, folded edges, edging, piping, hemmed edges, etc.
3 ) Gluing process: It refers to the process of gluing the lining material into a whole through an adhesive.
4 ) Basic sewing technology: It is the main means to connect all parts of the product. Only by sewing can the scattered parts be assembled into a complete product.

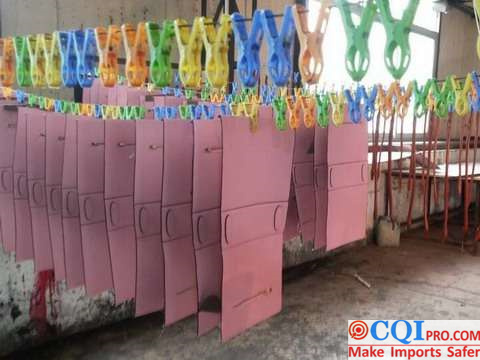
Common Defects In Backpack Inspection And Their Causes
Appearance class:
- Fabric drawnwork, thread thickness, perforation, pinhole, etc. ( Usually due to poor quality of raw materials and improper handling of cloth ).
- sewing needle bursting, needle jumping, needle leakage, bending, etc. ( Usually due to improper operation of workers or improper debugging of equipment ).
- The zipper is not smooth, damaged, scratched, rusted, and has sharp edges. ( usually due to improper material selection or long storage time, bruised during installation ).
- The viscosity of hook and loop is poor, and the corresponding two hook and loop pieces are dislocated. ( Usually due to poor quality hook and loop, stitching error ).
- The internal nails shall be round and smooth and shall not crack. ( Usually due to improper operation when fixing the process ).
- The screen printing of LOGO is unclear, and the thickness is uneven after molding; The thickness of embroidery is uneven, and the embroidery thread is easy to loosen. ( Usually due to the poor quality of silk-screen printing ink, the embroidery operation is improper ).
- The label is not wrinkled and easy to fall off. ( Usually due to insufficient stitching ).
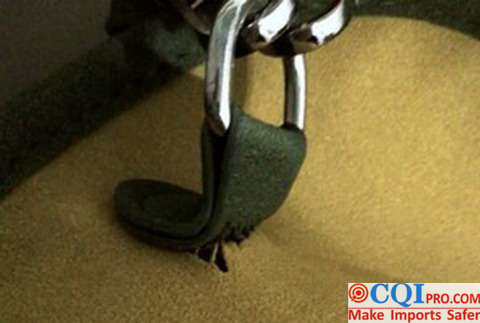
Function class:
- Shoulder straps and handles must have sufficient bearing capacity; ( Usually, the sewing is not in place due to poor fabric quality ).
- All accessories can be used normally.
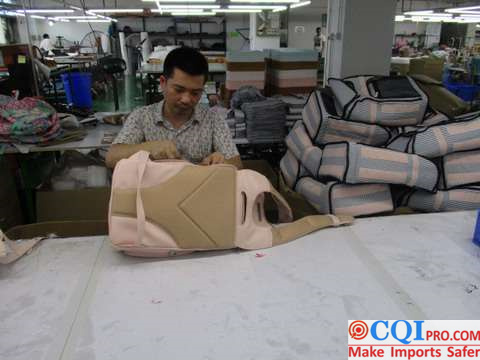
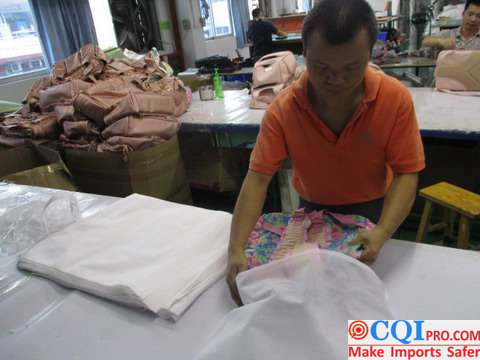
Backpack Inspection-Product Testing
Inspector spot test in backpack inspection
- Appearance neatness and product surface: Observe the product surface under natural light or fluorescent lamp.
- Color and printing: Observe the color of the product under natural light or fluorescent lamp, check the color of the product, or compare with the samples with a customer signature, so that customer can see the quality visually.
- Metal fittings: Observe metal fittings under natural light or fluorescent lamp, without rust, whether they are safe and firm, and the metal edges can not have sharp edges, etc., so that users can be injured, and whether the plating is even and smooth.
- Sewing: Observe sewing process and materials under natural light or fluorescent light, and check every detail in backpack inspection.
- Product shape: Observe the product shape under natural light or fluorescent lamp.
- Practical function test: Assemble the straps to test the back and check the actual length of the straps.
- Functional testing of accessories: Check the functional testing of zippers, buttons, hook and loop or chicken eyes of each sample product.
- Abuse Test: Repeat 20 times for sewing, bartack, zipper, button, hook and loop or chicken eye. No damage is found. Pay attention to unilateral pulling of zipper and check sewing strength, 3-5pcs for each item.
- Tension test: Conduct tension tests on seams, fittings,bartack,handles, shoulder straps or straps to check whether the stitches are firm. If large goods have tassels, they must be firm and not easily dropped. The length must be consistent and level. The strength should be used for pulling test in backpack inspection.
- Strap strength test: select 5-15 kgs load to test the strap strength according to the size of the product and lift the strap for 2 hours.
- Tests for color fastness: Check whether the dry rubbing and wet rubbing on the surface will fade and whether the product will fade.
- 3M test of printing: firmly stick the part to be tested with 3M adhesive tape, grasp one end of the adhesive tape by hand, quickly pull off the adhesive tape in the vertical direction ( 90°).Perform the same test twice at the same position.
- Check the number of stitches: Measure the number of stitches per inch with a ruler or tape measure and record it.
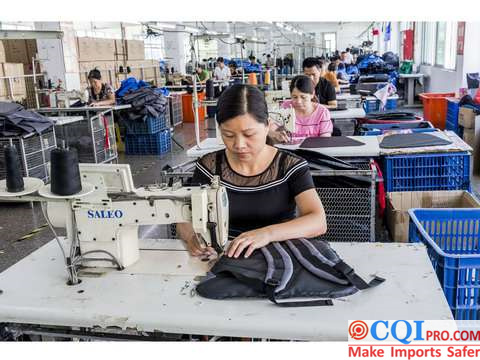
Laboratory testing
- Limit of harmful substances: The limit value of harmful substances in leather, fur and regenerated leather materials shall conform to the national standard GB20400; The limit of harmful substances in PVC artificial leather materials shall conform to the national standard GB21550; The limit of harmful substances in textile materials and adhesive for bags shall conform to the standard QB/T 1333.
- Physical and mechanical properties: vibration impact property, bag lock durability, fastener durability, zipper durability, sewing strength, plastic snap durability, rubbing color fastness, hardware fittings corrosion resistance, strap folding resistance, etc. shall conform to the standard QB/T 1333.
CQI5 is committed to providing importers worldwide with product quality inspection services that far exceed those of our peers. If you are planning to import or have imported from China or Southeast Asian countries, please contact us cs’@’cqipro.com to learn more about how we can make your imports safer.
This article is an original article for CQI Inspection, who is committed to providing high-quality product inspection technology and know-how sharing for global importers and retailers to make imports safer.
All rights reserved. The contents of this website provided by CQI Inspection may not be reproduced or used without express permission.
For reprint, please contact with CQI Inspection, thank you.