Adapter Production Process, Safe Production in China
The adapter is a product of modern power electronics technology, which maintains a stable output voltage with the help of controlling the time ratio of switching tube enable and disable. Due to the progress of power electronics technology, adapter technology has also advanced with the times, with the advantages of high efficiency, low power consumption, compactness, light weight, etc., representing the development direction of the voltage stabilization power supply. In addition to the product design and development, manufacturing is also an important part of ensuring the quality of the adapter. Only the adoption of rigorous production processes and standards can make the completed adapter to achieve the expected performance and results.
The following is a specific description of the manufacturing process of the adapter module and the standards of each link and the matters that need attention.
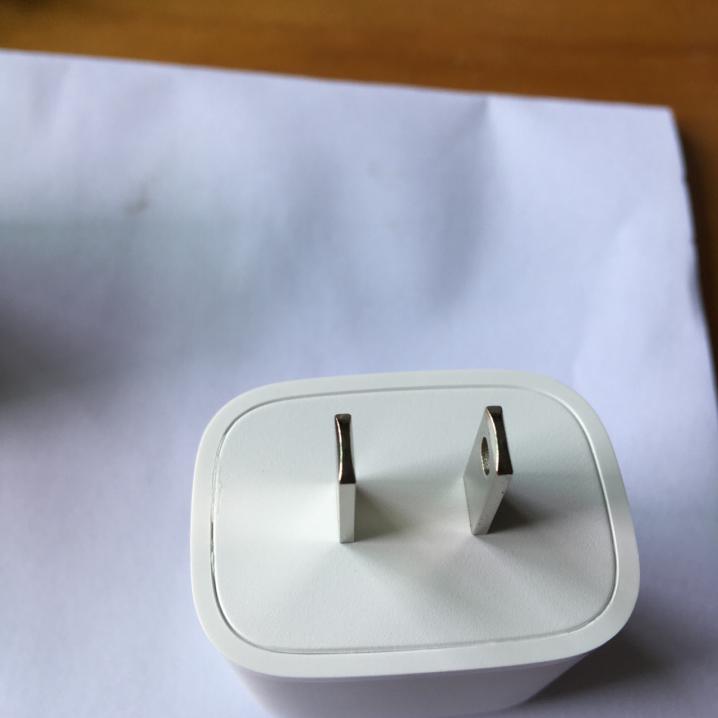
1. Adapter production process – pre-production preparation
In order to ensure the smooth manufacturing of the product and to complete the manufacturing operation with high efficiency and quality, it is necessary to make pre-production preparation in advance and in strict accordance with the relevant technical documents. Mainly including: the preparation of components, raw materials and related equipment required; the design documents, process documents, test methods and manufacturing operation regulations of the relevant adapters; the need to complete the assembly of some components and the performance inspection of relevant components in advance.
2. Adapter production process – coil making
Strictly speaking, coil making is also part of the pre-production preparation, but the magnetic device is very critical to the power adapter and directly affects the product performance, so it is listed separately and the operator needs to have the magnetic device induction qualification. Determine the winding and performance parameters before winding the coil, determine the material table according to the standard of magnetic devices, select the enameled wire and skeleton according to the performance parameters of magnetic devices winding, and cut the size of each winding wire. The skeleton will be fixed on the winding machine for winding. Special attention should be paid to the following matters: the winding should be tight and flat; the incoming wire should be short and the outgoing wire should be long; the primary wire should be first and the secondary wire should be second; if there are two secondary windings with the same number of turns, they should be wound at the same time, while the number of turns should be different, they should be wound separately. Finally, the incoming and outgoing wires of each winding are twisted 3-5 times to avoid loosening, and then the skeleton is taken off the winding machine, finishing the enameled wire, scraping the wire and tin.
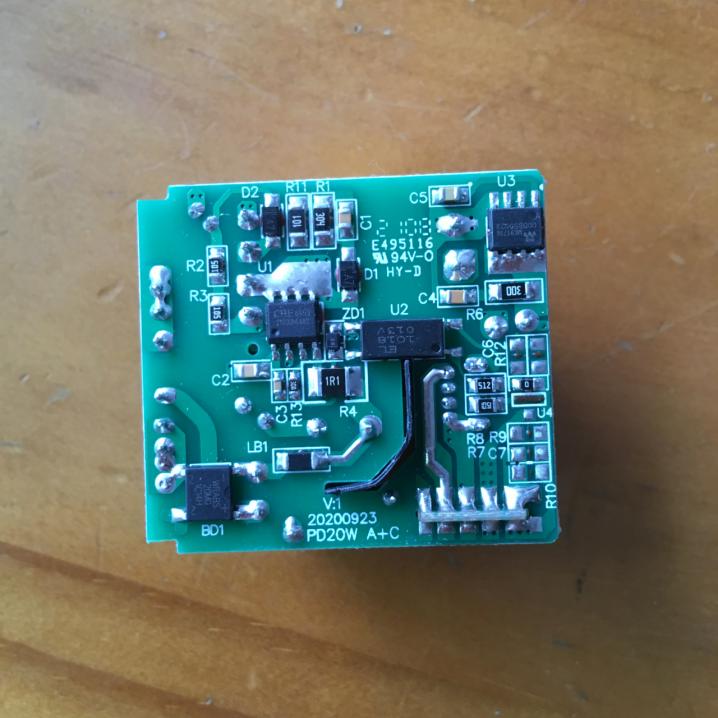
3. Component welding assembly
Standard component welding is the basic guarantee of product quality. It stipulates that there is no leakage of components, each solder joint is solidly welded, good contact, and no solder error parts. In the welding process to do: determine the accuracy of the raw materials; soldering iron to fully preheat, one hand holding the iron, one hand holding tweezers or wire; welding to have the order, such as from large to small, from left to right, etc.; each welding a component need to check, check whether it is solid, contact is good, not to appear offset, desoldering, false welding, solder joints should be smooth, round, should not have bad phenomena such as burrs; also need to check There is no leakage of welding and short circuit of components due to solder flow; chips, capacitors, resistors should be close to the surface of the substrate.
4. Cleaning
Cleaning refers to the use of ultrasonic cleaning machine to clean the substrate, to ensure that the product without excess solder paste, no impurities, cleaning 2 times is appropriate. Operation should ensure that the installation of cleaning equipment is stable, according to the standard process of pouring water and wash board water respectively, cleaning 1 minute. After cleaning, dry at room temperature or dry in a high-temperature drying oven, test the clean substrate to see if there is no false solder, false solder, empty solder, short circuit, etc.
5. Inspection
Any production process inspection is an indispensable process, but also the last quality assurance before the product is shipped. Power adapter inspection mainly includes routine appearance inspection, performance test and high and low temperature test.
Conventional test is to inspect the packaging and appearance of the adapter, should be free of damage, scratches, dirt, pin skew and other undesirable phenomena; the power adapter will be placed under a 1.5-10 times microscope to ensure that the plating is free of peeling, blistering, no fracture of the lead, rust and corrosion; use vernier calipers to test the physical dimensions. According to the customer agreement, test the input and output parameters, load transients, input voltage transients, to see if the output is all in line with the requirements.
High-temperature test is to place the power adapter in a high-temperature drying oven to bake more than 2H, and then quickly remove the product for performance testing; low-temperature test is to place the adapter in a low-temperature storage box to freeze more than 2H, and then quickly remove the product for performance testing.
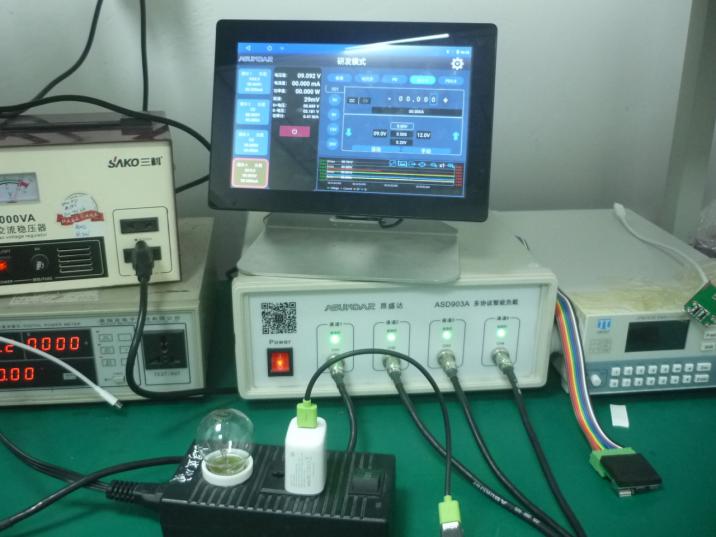
6. Glue filling
Gluing is also to slowly inject the refrigerated gel into the body, the gel should not exceed the components, the surface should be smooth and flat. The product is placed in parallel in the tray after filling, and solidified at room temperature for more than 48 H. The gel is completely solidified before the next operation. After the product is potted into one, the anti-vibration performance is improved to ensure the quality of the product.
7. Shell sealing
The sealing shell adopts parallel seam welder. First place the product base in the fixture of the parallel seam welder, then take the cover plate and place it on the product base to confirm the direction of the cover plate. According to the size of the shell to be welded, enter the corresponding length and width of the shell and the height of the left and right electrodes on the interface of the welding parameters, and after setting all the parameters, carry out spot welding work. After all the welding work is finished, the welding surface should be inspected under a microscope of 20-40 times. The welding should meet the following requirements: the welding surface is well welded, there should be no porosity, cracks, unsealed, cover deviation and other undesirable phenomena; the welding surface is flat, there should be no unevenness, wheel marks; the welding surface should not be over-burned and scratched.
8. Marking
Marking is the last step before product shipment, marking the product, so that the product model, pin function is easy to identify, to avoid misconnection, misuse.
CQI5 is committed to providing importers worldwide with product quality inspection services that far exceed those of our peers. If you are planning to import or have imported from China or Southeast Asian countries, please contact us cs’@’cqipro.com to learn more about how we can make your imports safer.
This article is an original article for CQI Inspection, who is committed to providing high-quality product inspection technology and know-how sharing for global importers and retailers to make imports safer.
All rights reserved. The contents of this website provided by CQI Inspection may not be reproduced or used without express permission.
For reprint, please contact with CQI Inspection, thank you.