Overview of Meltblown Fabric Machine and Analysis on Process
Meltblown fabric is the key material for filtering in the mask and is the heart of the mask. In addition to blocking large dust particles, it can also absorb fine dust, bacteria and virus droplets through electrostatic charges on the surface. With many voids, fluffy structure and good crease-resistant,these superfine fibers with unique capillary structure increase the number and surface area of fibers per unit area, thus making meltblown fabric have good filterability, shielding, thermal insulation and oil absorption. Therefore, a good meltblown fabric machine is also crucial to produce qualified and high-quality protective masks.
Meltblown fabric is a melt-blown nonwoven fabric formed by drawing the polymer melt trickle extruded from the die spinneret orifice with high-speed hot air flow, thereby forming superfine fibers and collecting the superfine fibers on a screen or roller, and simultaneously bonding the superfine fibers by itself. The width of meltblown fabric produced by normal China meltblown fabric machine manufacturers is generally 1600mm, 2400mm and 3200mm, and the diameter of extruder is usually 90mm, 105mm and 135 mm. However, after the epidemic began, the kind of minicomputers,which were used in Yangzhong’s family workshops rush headlong into mass action.The width was smaller, usually only a few tens of centimeters, and the screw diameters were mostly 45mm, 50mm and 65 mm.
This kind of meltblown fabric machine has low output and low quality, but the cost is cheap, delivery time is fast.The price before the epidemic was 20,000-30,000RMB. Now it has risen to over 200,000RMB, but it is still much cheaper than normal extruder of meltblown fabric manufacturer. At present, the main melt-blown extruders produced 1600 sold by regular large factories in the market are priced at more than 6 million, and the delivery time is more than 2 months. However, due to the improvement of the global epidemic situation, and the Chinese government is more and more strict with export of Chinese masks,the price expectation of meltblown fabric machine is uncertain.
Meltblown Fabric Production Process
Meltblown fabric production in the middle part of the industry chain mainly includes six processes: melt preparation, filtration, metering, melt extrusion from spinneret orifices, melt trickle drafting and cooling,and netting.
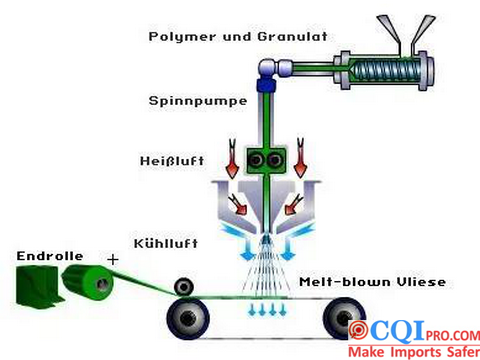
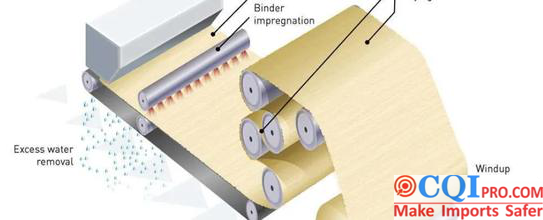
Overview and Principles of Meltblown Fabric Machine
Meltblowing is a method of preparing fibers by blowing polymer melt with high temperature and high speed air flow to make it stretch rapidly.After the polymer slices are heated and pressurized by a screw extruder to a molten state,the polymer slices reach a spinneret hole at the front end of a nozzle through a melt distribution flow channel, and after extrusion, the polymer slices are thinned by stretching of two converging high-speed and high-temperature gas streams.The refined fibers are cooled and solidified on a net curtain device to form meltblown nonwoven fabric.
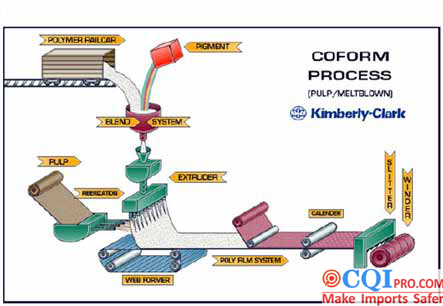
Components of Meltblown Fabric Machine
Melting nozzle, automatic charging system equipment components, ultrasonic cleaning machine, air heater, centrifugal fan, screw extruder, meltblown netting machine, meltblown offline winder, meltblown offline slitting machine and other key equipment.
The spinneret is the core component of meltblown fabric machine.The spinneret for melt spinning is a representative spinneret for the manufacture of synthetic fibers such as terylene and chinlon. Thermoplastic resin is heated and melted, extruded through the spinneret at a certain speed in air or water, and cooled and solidified into fibers. One of the most core technologies is the small nozzle on the spinneret.
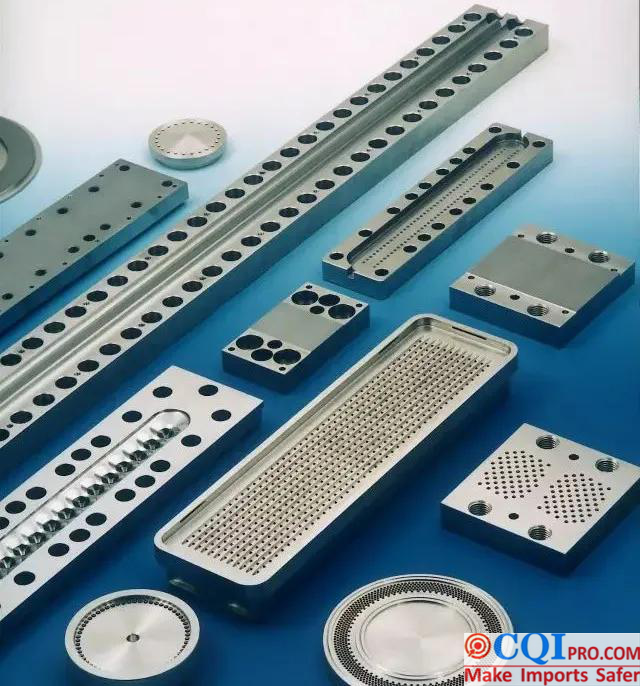
This kind of nozzle is not only small in size with 0.15mm, but also can process complex hole patterns on such a small nozzle, which is extremely difficult to process, and the nozzle processing takes several months.If the processing precision is not high,the meltblown fabric finally cannot meet the corresponding technical requirements,which will affect the protective performance of the mask.
Structure of meltblown fabric spinneret
The structure of the spinneret is divided into three forms: circular,fan-shaped and rectangular according to the shape of the spinneret.At present,circular plates and rectangular plates are widely used at home and abroad. In order to be suitable for different kinds of chemical fiber spinning occasions, circular spinnerets are divided into flat plate type, flange flat plate type, flat plate ring type, flange ring type, etc. Rectangular spinnerets are divided into flange rectangle and flange groove rectangle, etc., which are mostly used for short fiber spinning with more holes.
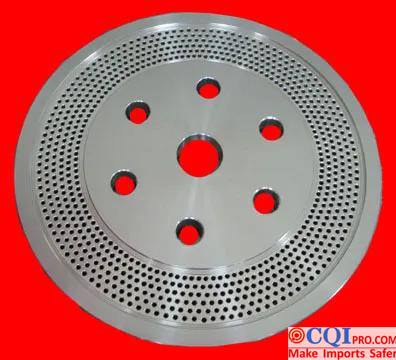
Meltblown Die
The die head comprises a main body, a spinneret plate and an air plate.The spinneret plate and the air plate are detachably installed in the die head main body.A spinneret hole is arranged in the spinneret plate.A plurality of crevice grooves are arranged between the spinneret plate and the air plate.A plurality of gas flow channels are also arranged in the die head main body. The gas flow channels are communicated with the crevice grooves.An air pipe connecting end is arranged on the outer wall of the die head main body.The air pipe connecting end is communicated with the gas collecting chamber through an air pipe.One end face of the spinneret hole of the spinneret plate is fixedly connected with a spacing flow stabilizing piece and the other end face of the spinneret hole is fixedly connected with each other end face.
In meltblown fabric machine, melt blowing die is one of the core components to realize high polymer wire drawing. The design and precision directly affect the length, uniformity, toughness, fineness and other aspects of wire drawing, thus having a decisive impact on the final coil quality.
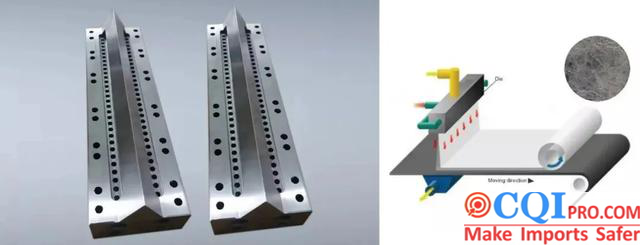
Meltblown Fabric Machine Air Heater
That is the pipeline heater consists of a main body and a control system. The heating element adopts stainless steel pipe as a protective sleeve, high temperature resistance alloy wire and crystalline magnesium oxide powder. After compression molding, the control part adopts advanced digital circuit, integrated circuit trigger and high reverse pressure silicon controlled rectifier to form an adjustable temperature measurement and constant temperature system, which ensures the normal operation of the electric heater.
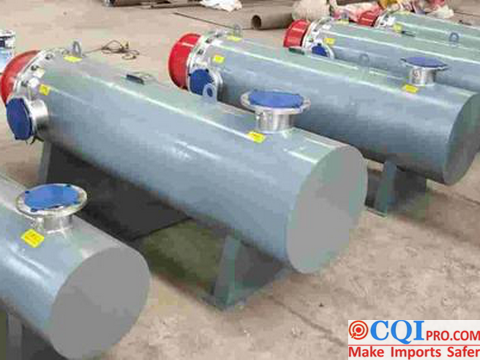
Polypropylene Raw Materials
Polypropylene material is refined from petroleum. At present, Sinopec and other enterprises can produce large quantities of polypropylene. However, the equipment for producing polypropylene into meltblown fabric, especially the spinneret,the core component,is mainly imported. These suppliers mainly include Carson spinneret in Japan, Enka in Germany, Japanese spinneret and other enterprises. Japanese suppliers occupy the most important position. At present, the output of several enterprises is far from meeting the market demand.
Therefore, the production capacity of the mask ultimately depends on the output of meltblown fabric production equipment, while the production of the spinneret nozzle, the core of meltblown fabric machine, is very difficult. The processing time takes several months. The output cannot be greatly increased in a short period of time, and the production capacity is very limited. This also makes the mask production can only make maximum use of the current equipment and increase production by extending the working time of the production line.
Configuration of Main Devices
- Screw extruder
- Metering pump
- Meltblowing device
- Receiving network
- Winding device
- Feeding device
The continuous production line of meltblown nonwovens is about 6m high, 5m wide and 20m long. Its production equipment is as follows:
(1) Screw extruder: the diameter of the screw is generally 100-120 mm, and the length/diameter ratio is 30.The purpose is to melt the slices.
(2) Metering pump:the function is to accurately measure, control the output and fiber fineness. It is a gear pump to continuously convey melt to spinneret.
(3) Melt filter: the function is to filter out impurities in the melt so as not to block the spinneret orifice.
(4) Conveying net curtain: melt blown fibers are evenly received and spread on the net and transported forward, and a suction fan is arranged below the melt blown fibers to discharge hot air from above.
(5) Spinning box: It is the key equipment of melt blowing process. It has a long strip spinneret plate, which is full of a long row of spinneret holes, generally about 1500 orifices per meter long. Hot air spray pipes are installed on both sides of the spinneret plate, and hot air spray holes are installed under the spinneret plate at an angle of 50b with the spinneret holes, so that after fibers are sprayed out, high-speed hot air is immediately used for airflow stretching to break the fibers into superfine fibers.
(6) Feeding system: it consists of three measuring hoppers, which are respectively used for measuring white slices, color masterbatches and additives. The three components enter the mixing stirrer below to mix evenly and are put into production.
(7) The coiler adopts full-automatic coiler to coil and package meltblown fabric. Meltblown nonwovens are characterized by ultra-fine fibers with a minimum fiber diameter of 0.5Lm, generally between 1 and 5 lm. The finer the fiber, the better the quality of meltblown fabric, but the yield is relatively reduced. Because the fiber is ultra-fine, the specific surface area is large and the adsorption capacity is strong. Filtration efficiency of meltblown fabric is high, which is the most prominent advantage of meltblown fabric.
(8) Hot air blower and heater: provide the temperature and pressure of hot air used in spinning air flow drawing, which is electrically heated and consumes a large amount of electricity.
CQI5 is committed to providing importers worldwide with product quality inspection services that far exceed those of our peers. If you are planning to import or have imported from China or Southeast Asian countries, please contact us cs’@’cqipro.com to learn more about how we can make your imports safer.
This article is an original article for CQI Inspection, who is committed to providing high-quality product inspection technology and know-how sharing for global importers and retailers to make imports safer.
All rights reserved. The contents of this website provided by CQI Inspection may not be reproduced or used without express permission.
For reprint, please contact with CQI Inspection, thank you.