Power Adapter Inspection Standards, Summary by a Chinese Factory Technician
The role of the power adapter is to convert the high voltage at home into a stable low voltage of about 5 volts to 20 volts for these electronic products to work properly, generally by the shell, transformer, inductor, capacitor, control IC, PCB board and other components, its working principle is converted from AC input to DC output; according to the connection method can be divided into wall adapter and desktop adapter.For more information on the production process of power adapters, please refer to this article:Adapter Production Process, Safe Production in China
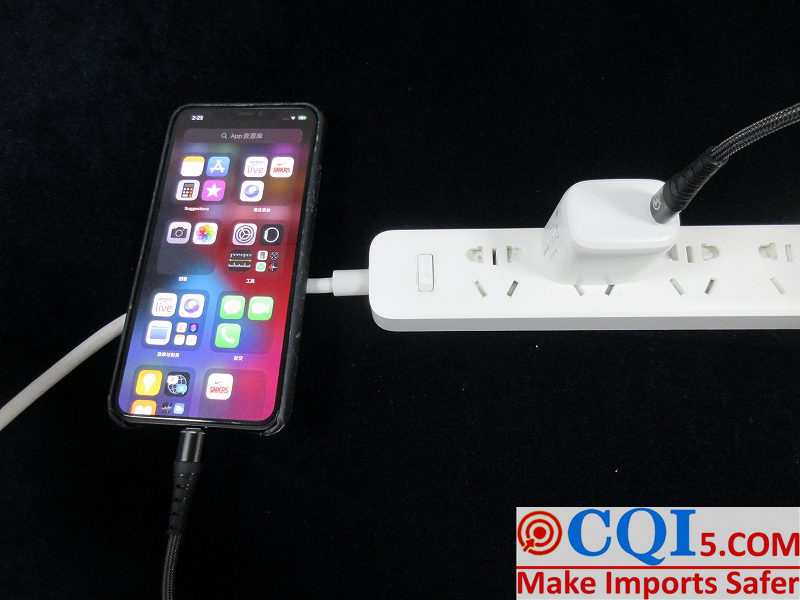
1. Power adapter inspection standards – short circuit test
Test description:
Short circuit the module output in various input and output states, the module should be able to achieve protection or retraction, repeatedly short circuit several times, after the fault is removed, the module should be able to automatically resume normal operation.
Test method:
No-load to short-circuit: Within the full range of input voltage, short-circuit the module from no-load to short-circuit, the module should be able to achieve output current limiting or retraction normally, after short-circuit elimination, the module should be able to resume normal operation. Let the module work repeatedly from no-load to short-circuit constantly, with a short-circuit time of 1s, a release time of 1s and a duration of 2 hours. After this, the short circuit is released and the module is judged to be able to work properly.
2. Power adapter inspection standards – repeated switching test
Test description:
Power module output with maximum load, the input voltage is 220v, respectively, (input overvoltage point -5v) and (input undervoltage point +5v) conditions, input repeated switching, test the performance of the power module repeated switching.
Test methods:
1) input voltage of 220v, power supply module fast with maximum load, voltage input controlled by contactor, closed for 15s, disconnected for 5s (or can be simulated with ac source), continuous operation for 2 hours, power supply module should work normally.
2) input voltage is overvoltage point -5v, power module with maximum load, control voltage input with contactor, close for 15s, close for 5s (or can be simulated with ac source), continuous operation for 2 hours, power module should work normally.
3) input voltage is under voltage point -5v, power supply module with maximum load, use contactor to control the voltage input, close 15s, disconnect 5s (or can be simulated with ac source), continuous operation for 2 hours, the power supply module should be able to work normally.
In the above test, the power supply module works normally, the power supply module can work normally after the test, no obvious changes in performance, qualified; otherwise failed.
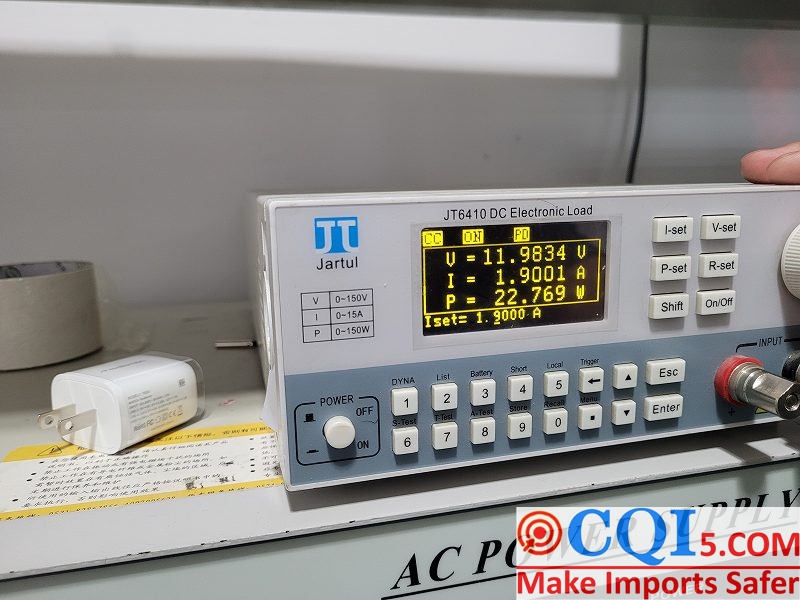

3. Power adapter inspection standards – input low voltage point cycle test
Test description:
A power adapter input undervoltage point protection of the setting back poor, often occurring in the following situations: input voltage is low, close to a power module undervoltage point off, undervoltage when carrying a load, after power failure, due to the power supply internal resistance, the voltage will rise after the load is removed, may cause a power module in the state of repeated development at low voltage.
Test method:
Power adapter with full load operation, input voltage from (input undervoltage point -3v) to (input undervoltage point + 3v) slowly change, time set to 5 ~ 8 minutes, repeated cyclic operation, the power supply module should be able to work normally and stably, continuous operation for at least 0.5 hours, no significant changes in the performance of the power supply module.
A power adapter normal continuous operation, at least 0.5 hours after the performance of no significant changes, qualified; otherwise failed.
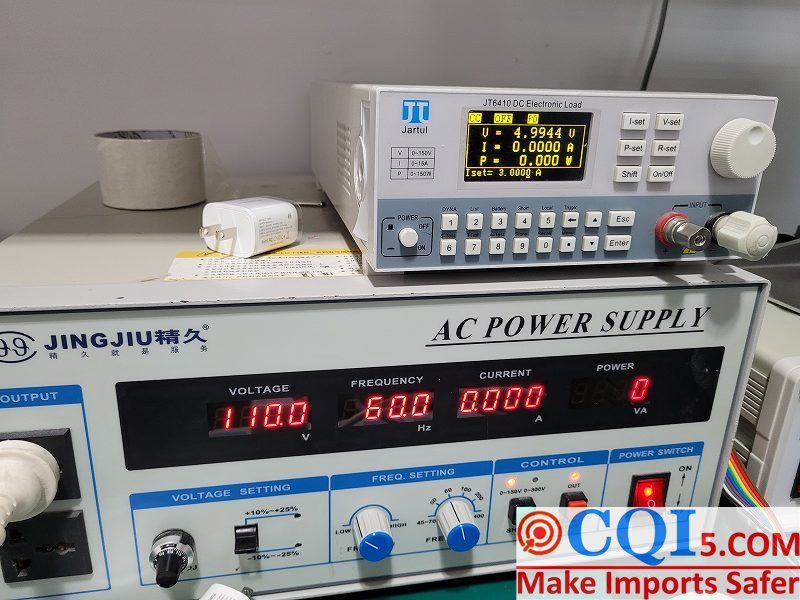
4. Power adapter inspection standards – input transient high voltage test
Test description:
The pfc circuit uses an average circuit for over-undervoltage protection, so when input transient high voltage, the pfc circuit may quickly achieve protection, thus causing damage, test the stable operation capability of the primary power adapter under transient conditions to assess reliability.
Test method:
1) Rated voltage input, test the input voltage waveform with a dual trace oscilloscope to match the overvoltage protection signal, the input voltage jumps from the power limit point plus 5v to 300v, read out the cycle number n of 300v before overvoltage protection from the oscilloscope as the basis for the following test.
2) Rated input voltage, power adapter with full load operation, superimposed on the input 300v voltage jump, superimposed on the number of cycles (n-1), superimposed on the frequency of 1 time / 30s, a total of 3 hours of operation.
Power adapter in the above conditions can be stable operation, does not appear damage or other abnormal phenomena, qualified; otherwise failed.
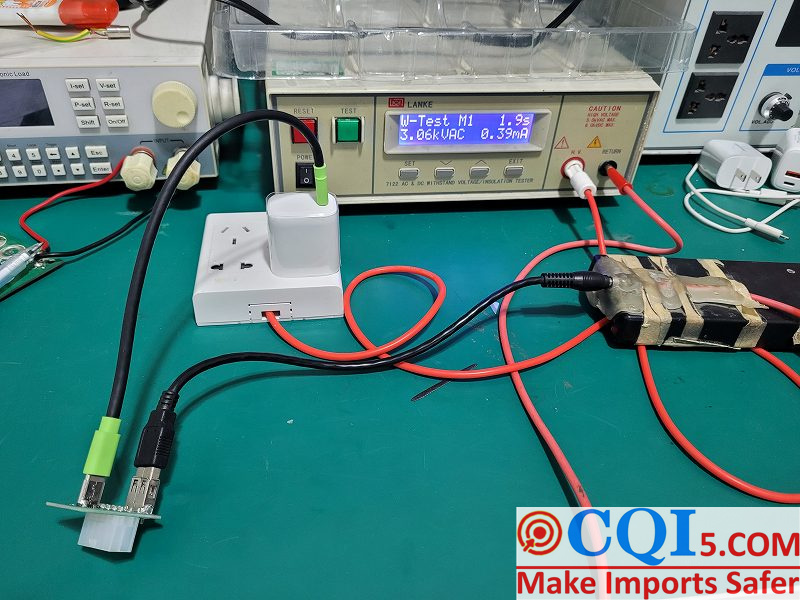
5. Power adapter inspection standards – input voltage dips and output dynamic load
Test description:
A module in the actual use of the process, when the input voltage dip, the power adapter sudden load limit is possible, when the power device, magnetic components work in the maximum transient current state, the test can test the control timing, current limit protection and other circuit and software design rationality.
Test method:
1) adjust the input voltage to jump between the undervoltage point +5v (duration 5s), overvoltage point -5v (duration 5s), the output is adjusted to jump between the maximum load (maximum rated capacity, duration 500ms), no load (duration 500ms), run for 1 hour.
2) Adjust the input voltage to jump between the undervoltage point +5v (duration 5s), overvoltage point -5v (duration 5s) and the output is adjusted to jump between maximum load (maximum rated capacity, duration 1s), no load (duration 500ms) and run for 1 hour.
Under the above conditions, it should be able to run stably without damage or other abnormalities, pass; otherwise fail. If damage occurs, record the fault problem to provide a basis for analysis of the cause of the damage.
CQI5 is committed to providing importers worldwide with product quality inspection services that far exceed those of our peers. If you are planning to import or have imported from China or Southeast Asian countries, please contact us cs’@’cqipro.com to learn more about how we can make your imports safer.
This article is an original article for CQI Inspection, who is committed to providing high-quality product inspection technology and know-how sharing for global importers and retailers to make imports safer.
All rights reserved. The contents of this website provided by CQI Inspection may not be reproduced or used without express permission.
For reprint, please contact with CQI Inspection, thank you.