Do You Know About Glass Cup Inspection Standards And Tests
1.Purpose:
In order to clarify the inspection specifications and requirements of CQI Inspection Company for glass cup inspection standards, this product inspection requirement is specially written to standardize the company’s quality inspection service level for customers.
2.Scope of application:
This inspection technical document is used to standardize the pre-shipment inspection service of glass cup.
3.Defect definition for glass cup inspection:
Serious defects (CRT): the user’s life is a major hazard or has the potential to harm and violate the relevant safety requirements of defects
Major defects (MAJ): affect the use of the product, reduce product reliability and service life or seriously affect the product image defects
Minor defects ((MIN): the product has a slight appearance defects and does not affect the product function defects
4.The level of inspection:
Sampling standards: MIL-STD-105E
Acceptance level (AQL): CR=O MA=1.5 MI=4.0
5.Common appearance and functional defects for glass cup inspection
1.Foreign objects:
not allow to be contaminated by rust, oil stains and water stains that are difficult to erase, and there are no foreign objects such as scraps of paper, insects, hair, broken glass, metal, and a large amount of dust in the bottle.
2.Bottle top:
no big mouth, small mouth, crack, breakage or burr on the bottle mouth; Bottleneck has no obvious skew or shift, which affects filling and matching.
3.Thread :
threads should be smooth and level off, without deformation, deformity and roughness.
4.Clamping line :
not have obvious protrusion, dislocation of double clamping lines and sharp burr, etc., which will affect safety and compatibility.
5.Sitting position:
there is no concave-convex deformation at the bottom of the sitting bottle and it will affect the stability.
6.Thickness:
the thickness of the bottle body is even within the receiving range, and the thickness is not less than 1.5mm.
7.All parts of the bottle should not be cracked, cracked or damaged.
8.Heterochromatic spots :
the main view plane of 8 different color points allows I or 2 points with φ ≤ 0.5mm, but does not affect the LOGO and layout; 2 or 3 points of inattention with φ less than or equal to Φ≤0.5mm are allowed on the non-main view surface, but the layout is not affected.
9.Bubbles:
One or two bubbles with φ ≤ 0.5mm are allowed in the main plane of bubbles, but the LOGO and layout are not affected; Non-main view plane allows less than 3 bubbles with φ≤ 1mm and does not affect the layout; But no broken bubbles are allowed.
10.Holes:
I or 2 sand holes with φ ≤ 0.5mm are allowed on the main surface of sand holes, but the LOGO and layout are not affected; Non-main view plane allows less than 3 sand holes of φ ≤ 1mm and does not affect the layout.
11.Frosting:
frosting requires proper surface thickness and moderate thickness, and the position of frosting generally does not rise to the bottom of the thread, not lower than the junction between the bottleneck and the bottle body. There are no bright spots on the front of the bottle body, 5 bright spots on the side at most not exceeding 0.8mm and 5 bright spots on the bottom not exceeding 1.0mm.
12.Printing quality :
the content, font, deviation, color and size of patterns and characters must meet the requirements of standard samples, and the patterns or fonts must be neat and clear, without obvious font blur, color difference, shift, burr, misregister, etc.
13.Printing position:
if the printing position is less than 30ml, the upper and lower deviation is allowed to be ±0.5mm, and the deviation of left and right inclination is ±0.25mm;; More than 30ml, the allowable deviation of up and down is ±0.75mm, and the deviation of left and right inclination is 0.25mm.
6.Common Testing Items for Glass Cup Inspection
1.Tape Test :
stick the tape on the part to be tested, press it flat with your fingers, wait for about 30 seconds, pull the tape down quickly, and test it at the same position once.
2.Adhesion check:
100 small grids of 1mm×1mm are drawn on the test surface with a hundred-grid knife, and each line should be deep to the bottom of the paint, and then tested with 3M810 tape, with no more than one grid falling off.
3.Stability test (12-degree slope, dumping test) :
fill the container with tap water and tilt it 45. When pouring water continuously from the mouth, the water must flow out in a column shape, and it is not allowed to flow out of the mouth width or to the outer surface or bottom of the product.
4.Flatness test:
a piece of glass is used for the bottom flatness test, and the bottom flatness of ceramic products is 100% tested.
5.Alcohol soaking:
soak the glass bottle in 50% alcohol for 2 hours, and there is no abnormality.
6.Friction test :
bronzing parts are rubbed 50 times with filter paper, and there is no obvious abnormality.
7.Net content inspection:
use a measuring cylinder to measure a certain amount of water and fill it to the shoulder of the bottle, and calculate whether it meets the requirements of net content, and if necessary, use the actual contents for testing.
8.Specification inspection :
important dimensions such as outer diameter of bottle body, inner and outer diameter of bottle mouth, bottle height, outer diameter of screw thread and bayonet thickness are measured with vernier caliper and height ruler with minimum scale value of 0.01mm.
9.Material inspection:
the material inspection of glass bottles is compared with the standard samples, and the weighing method is used for detection.
10.Compatibility test :
bottle is manually matched with the cover (nozzle), gasket and inner bowl (inner plug), and it needs to rotate smoothly. The distance between the bottle caps is measured by the plug silicon.
11. Bottom leveling test:
put it on a flat plate and check whether the bottom is uneven.
12.Air tightness test :
add a certain amount of water into the bottle, assemble it with the cover (nozzle), gasket and inner bowl (inner plug), put it upside down in the vacuum box, and vacuum it to -0.08Mpa at normal temperature, and keep the negative vacuum pressure for 5 minutes without leakage.
13.Check and test the internal cracks of glass products (check 50), tap gently with a metal bar, and distinguish from the sound to see if there are internal dark cracks.
14.Water leakage test of glass container:
fill the container with 80% water, put it on a piece of white paper and leave it for at least 4 hours to see if there is water seepage at the bottom.
15.Microwave-resistant inspection (if the glass product can be microwave-applicable):
put the water in the glass into the microwave oven, and after 15 minutes of high fire, check whether the glass has cracks, etc.
16.Front edges:
in view of the problem of large quantities of front edges, this problem must be noted. At the same time, the glass products should be soaked with water on site, because it is easier to hurt your hands after the surface is covered with front edges.
7.Summary
The above is the specific content of the glass cup inspection standards, but with the continuous development of the product manufacturing industry and the adoption of new materials and new production processes, new types of quality problems and new product testing requirements will directly result. Therefore, it is necessary to update the glass cup inspection standards irregularly.
CQI5 is committed to providing importers worldwide with product quality inspection services that far exceed those of our peers. If you are planning to import or have imported from China or Southeast Asian countries, please contact us cs’@’cqipro.com to learn more about how we can make your imports safer.
This article is an original article for CQI Inspection, who is committed to providing high-quality product inspection technology and know-how sharing for global importers and retailers to make imports safer.
All rights reserved. The contents of this website provided by CQI Inspection may not be reproduced or used without express permission.
For reprint, please contact with CQI Inspection, thank you.
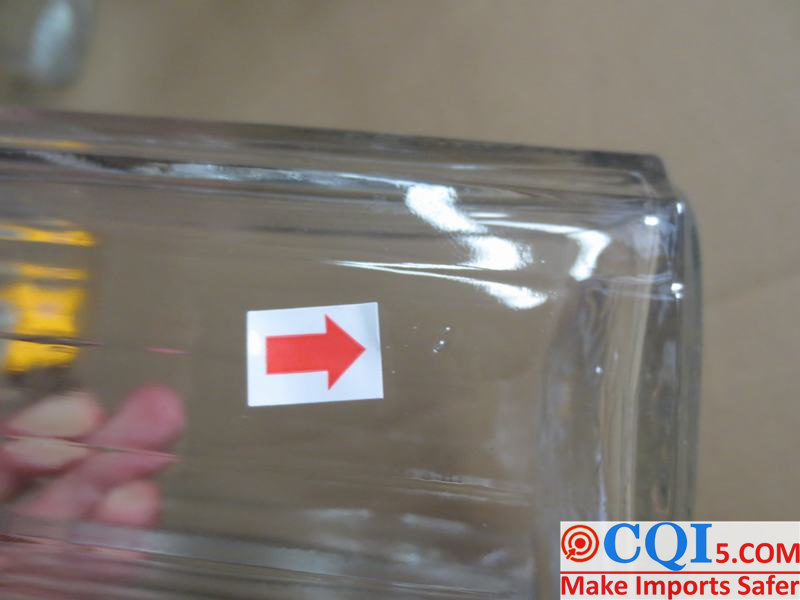
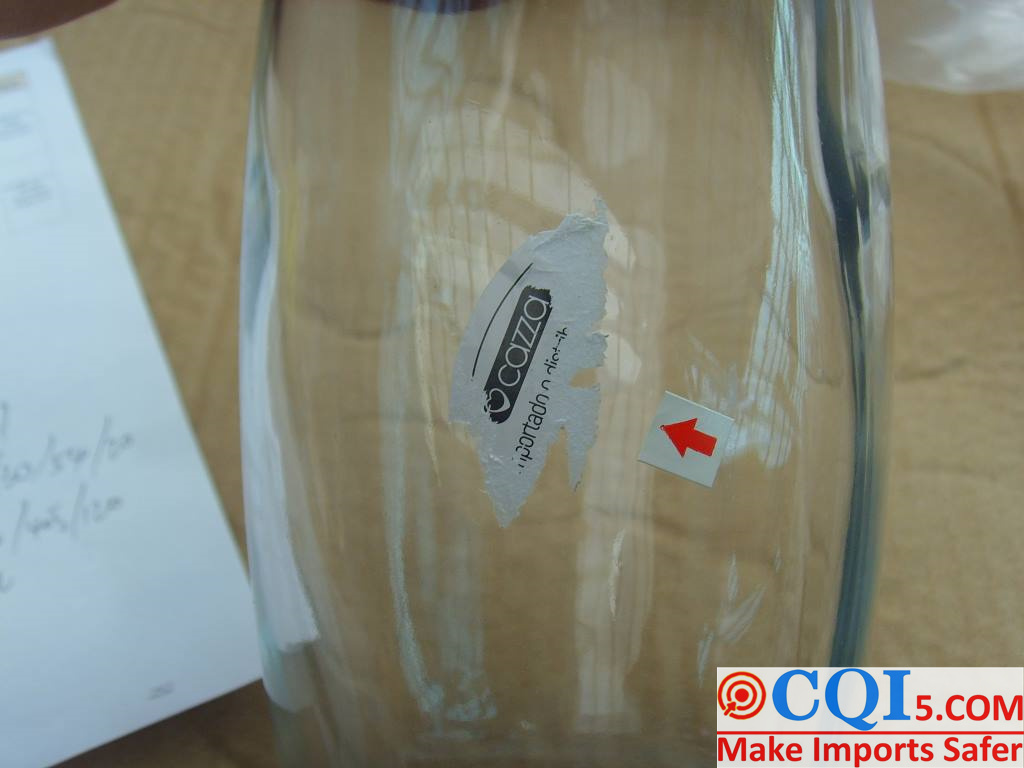

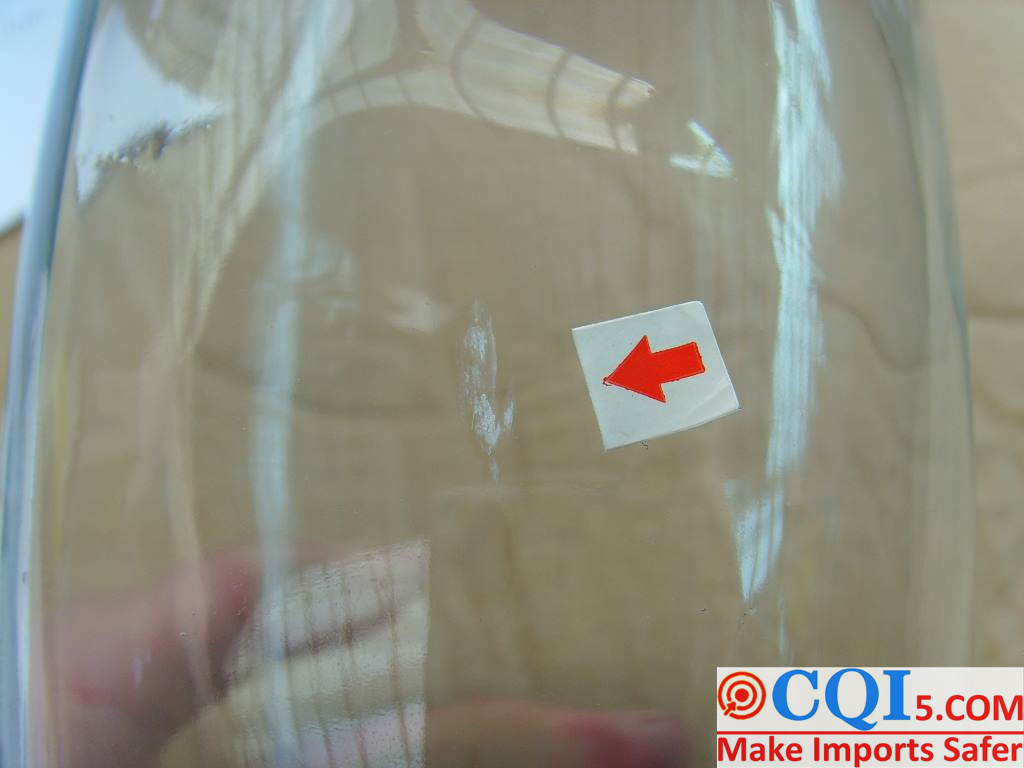
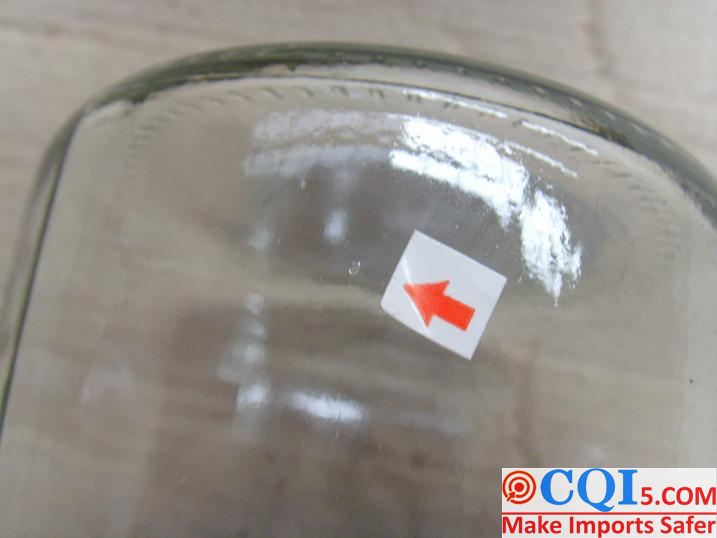
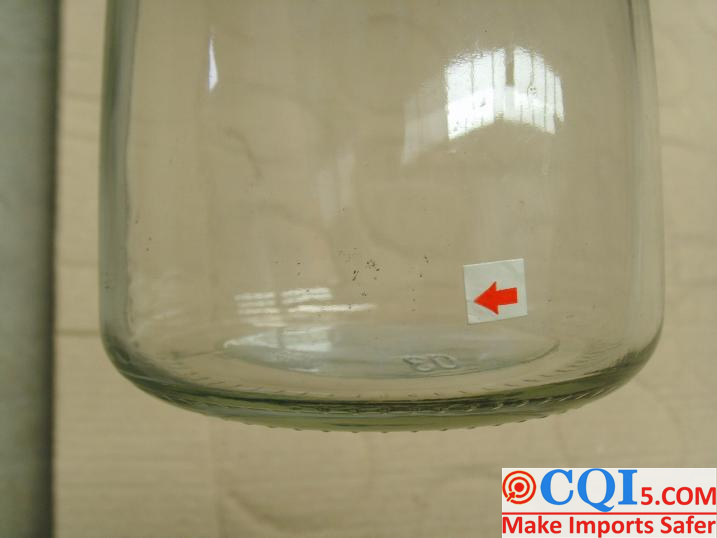